衢州熔模鑄造廠
發(fā)布時間:2024-02-20 01:41:02
衢州熔模鑄造廠
不銹鋼鑄件在進(jìn)行煅燒過程中,由于很多因素都會導(dǎo)致不銹鋼鑄件出現(xiàn)一些缺陷,精品起重配件也可能出現(xiàn)這種問題。在這個時候,有必要使用一些修復(fù)方法來恢復(fù)應(yīng)用,然后,鑄件制造商介紹了兩種不銹鋼鑄件缺陷的修復(fù)方法。修補(bǔ)方法:不銹鋼鑄件采用電焊焊接修復(fù),關(guān)鍵方法有手工電弧焊、氣體維護(hù)焊或氣保焊。清除方法:1)內(nèi)部缺陷,不銹鋼鑄件采用鏜銑床生產(chǎn)方法。2)表面缺陷,對于點(diǎn)分散表面缺陷,選擇手槍鉆或鏜銑床挖掘制造缺陷;對于砂孔,先放一根外國針頭敲砂孔松動,然后用鋁合金砂輪拋光。

衢州熔模鑄造廠
我國鑄件缺陷和技術(shù)相關(guān)原因分類,一般分類方法如下:第 一種是設(shè)計(jì)、工作和設(shè)計(jì)缺陷,因此原因是一個收縮階段,當(dāng)不能達(dá)到這一階段時,工具制造的鍛造商品存在缺陷。二是材料和冶煉。當(dāng)兩者不同時,缺陷是不可避免的。冶煉是由金屬和不銹鋼制品合金制成的。合理的特點(diǎn)是收縮很大,熱裂紋會很大。當(dāng)內(nèi)外缺陷得到改善時,鑄造過程也會造成錯誤。鑄造工藝知識缺陷造成的一個層面,那么裂痕和孔眼呢?砂缺陷的幾率能用工序開展操作,將缺陷的歸類和造型廢棄疏忽鑄件的缺陷。比如忘掉下芯的重量和偏差部分,抬箱使用情況下造成沙孔缺陷,適當(dāng)?shù)目刂撇攀峭醯馈?/p>
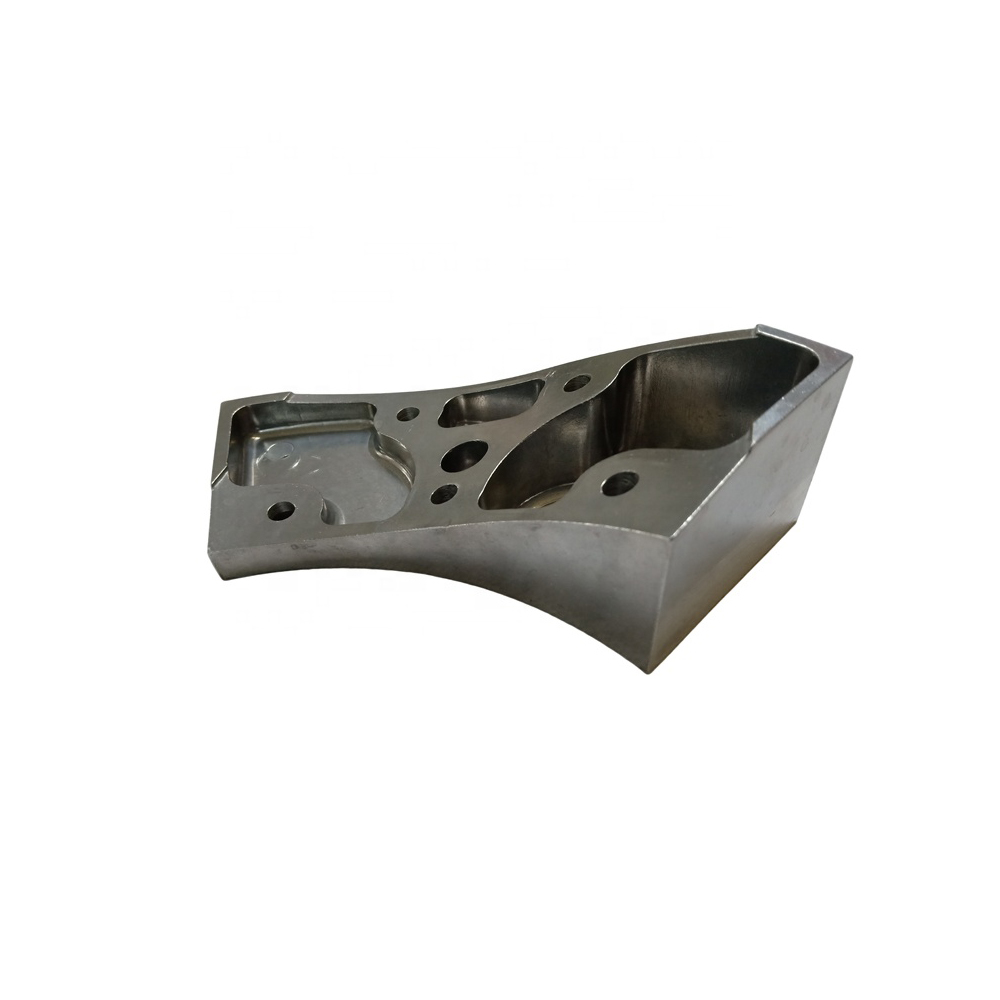
衢州熔模鑄造廠
當(dāng)含砂金屬鑄造、液態(tài)金屬填充、粘合劑分解、涂層干燥或金屬預(yù)熱不足時,會增加腔內(nèi)氣體量,當(dāng)腔內(nèi)氣體不能充分排出時,氣體停留在鑄造孔內(nèi),部分殘余氣體聚集在金屬鑄造墻與金屬液之間“氣阻”這些氣阻導(dǎo)致鑄件澆筑不足或冷隔缺陷。一方面,由于金屬鑄造涂層砂沒有妥協(xié)和透氣性,一方面,溴化鋰溶液中的氣體隨著溴化鋰溶液金屬的填充而減少;另一方面,它迅速明顯加熱,導(dǎo)致壓力升高,導(dǎo)致填充反壓力,阻礙溴化鋰溶液金屬填充腔。當(dāng)壓力超過一定極限時,氣體可能會打破金屬流液束的表面,根據(jù)內(nèi)澆口向外逃逸,破壞金屬液體的持續(xù)流動,導(dǎo)致明顯的氧化。當(dāng)氣體穿過金屬液體時,如果被初晶或凝結(jié)層阻擋,它將留在金屬液體中產(chǎn)生氣孔。

衢州熔模鑄造廠
不銹鋼板精密鑄件的應(yīng)用溫度合理,確保其溶劑在整個注射過程中具有特別好的循環(huán)。不銹鋼板精密鑄件的溫度應(yīng)根據(jù)注射間隔、冷卻過程、鋁合金、型號、規(guī)格、流量等因素來確定。在整個應(yīng)用過程中,不銹鋼板精密鑄件的物理性能高于鑄鐵,但原材料的鑄鐵性能較差。在整個生產(chǎn)過程中,不銹鋼板精密鑄件的溶點(diǎn)高于其他原材料。不銹鋼板精密鑄件的生產(chǎn)是其表面的關(guān)鍵缺陷。如果產(chǎn)品出現(xiàn)這樣的問題,在整個應(yīng)用過程中只選擇報(bào)費(fèi),會導(dǎo)致大家生產(chǎn)成本的增加,不利于產(chǎn)品資源的節(jié)約。

衢州熔模鑄造廠
磁粉檢測適用于檢測表面缺陷和表面下方數(shù)毫米深度的缺陷。在進(jìn)行檢測操作之前,必須使用直流(或交流)磁化設(shè)備和磁粉(或磁懸浮液)。鑄件內(nèi)外表面產(chǎn)生磁場的磁化設(shè)備,顯示缺陷的磁粉或磁懸浮液。如果鑄件在一定范圍內(nèi)產(chǎn)生磁場,磁化區(qū)域的缺陷會產(chǎn)生泄漏磁場。當(dāng)撒上磁粉或懸浮液時,磁粉會被吸收,從而顯示缺陷。顯示的缺陷基本上是橫向磁感應(yīng)線的缺陷,不能顯示與磁感應(yīng)線平行的條形缺陷。因此,在操作過程中,必須不斷改變磁化方向,以確保每個缺陷都能檢測到不明方向。

衢州熔模鑄造廠
大家知道鑄造件通用技術(shù)規(guī)定是什么嗎?下面鑄造件鑄造廠就來簡單介紹一下。鑄造件鑄造廠鑄造件通用技術(shù)規(guī)定:1、材料方面的規(guī)定。關(guān)鍵有強(qiáng)度、抗壓強(qiáng)度、延伸率、斷裂韌性。2、規(guī)格精度和形位精度。不同的鑄件有不同的要求,選擇不同的尺寸和幾何公差規(guī)格和公差等級。3、依據(jù)應(yīng)用規(guī)定,對鑄件的其他缺點(diǎn)要求驗(yàn)收要求。如氣孔、沙孔、縮松、縮松、焊瘤、夾砂、裂痕等。將液態(tài)金屬澆注到適合零件形狀和規(guī)格的鑄型腔中,冷卻凝結(jié),以獲得空白或零件稱為鑄件。